This article is a short overview of the most common cutters.
< Previous | List | Next >
Cutters come in a variety of types to allow different forms of cuts.
Cutter flute shape
The most common flute shapes are spiral and straight. The following table summarises the pros and cons of both types.
Cutter
|
Pros
|
Cons
|
Straight
|
|
|
Spiral
|
|
|
Spiral cutter
Spiral cutters have the flutes ground on a spiral around the cutter body. There are different types of spiral cutters depending on what direction the flutes are cut into the cutter.
Upcut spiral flute


The spiral orientation of flutes is in a clockwise direction (shown in yellow). Chip evacuation is in an upward direction (shown in brown). Material shear is also in an upward direction, which may not create a desired edge finish on the top surface of the cut.
Downcut spiral flute
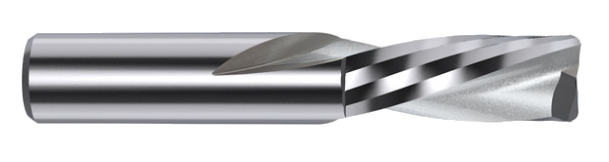

The spiral orientation of flutes is in an anti-clockwise direction (shown in yellow). Chip evacuation is in a downward direction (shown in brown). Material shear is also in a downward direction, which will create a good edge finish on the top surface of the cut, but not at the bottom.
Upcut and downcut spiral flute

This is a combination of upcut flutes at the tip of the cuter and downcut closer to the shank of the cutter.That’s a good choice for edge trimming plywood and hardwood.
Straight cutter

A straight cutter has a straight cutting edge. The quality of edge finish on top and bottom surface of the material is lower compared to the spiral cutters.

|
Straight cutters will not move chips away from the workpiece in the way that spiral cutters do. If using a straight cutter, ensure extraction is optimal.
|
Plunge features
Center cutting end mill
A center cutting end mill has cutting edges on both the end face of the cutter and the sides. It can be used for plunge milling (down direction cutting).

Non-center cutting end mill
A non-center cutting end mill has cutting edges on the sides and the cutting edges at the end of the tool do not overlap, which makes it impossible to do a straight plunge. A tool like this can only be used for side milling, if plunging is required it needs to ramp into the material.
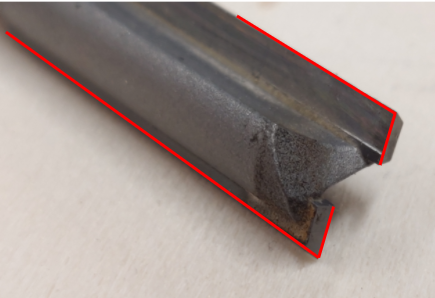
Most common types of cutters
End mill cutter

This is the most common milling cutter and is used for most general milling applications. It produces a sharp edge at the bottom of pockets and slots.
End mill cutters can be center cutting or non-center cutting.
Compression cutters
These have two sections, one to finish off the top face and the other to finish off the bottom face

Ball end mill cutter
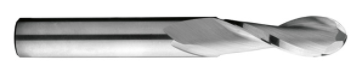
This type produces a radius at the bottom of pockets and slots. Ball end mills are used for contour milling and pocketing applications.
Engraving cutter
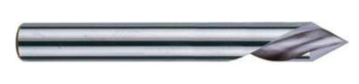
Engraving cutters come with a tip angle (included angle) varying from 30° to 90° and are used for contour engraving.
V-grooving cutter
A V-groove cutter is a type of cutting tool used in woodworking to create a V-shaped groove or channel in a workpiece.
Face mill
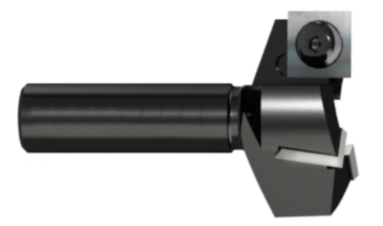
This type is a large diameter tool; it is used to cut a wide shallow path for facing operations.
Facing is used for machining a large flat area, typically the top of the part in preparation for other milling operations.
Cutter material
Cutters are normally made of HSS or carbide. The table below shows the advantages and disadvantages of the materials.
Cutter
|
Pros
|
Cons
|
HSS
|
|
|
Carbide
|
|
|
< Previous | List | Next >